Case Study
Problem:
A client that provides innovative electrified powertrain solutions for commercial transportation urgently required a vibration isolator with lower conductivity and unique specifications that did not exist at the time.
Solution:
The creation of a new, elastomeric compound and prototype to handle the large current emitted from the battery bank.
Results:
A custom product that offers impressive electrical resistance and was able to get to market ahead of time while exceeding all safety requirements.
A Low-Conductivity Elastomer Solution
The market for electric vehicles is advancing rapidly, as manufacturers attempt to keep pace with ever-tightening emissions requirements and reductions to address global climate change. In response, e-mobility development can come with some challenges, particularly if an existing process or part needs to be refined.
Such was the case for one of our clients, an innovative electrified powertrain solution provider for commercial transportation, who previously worked with our team to incorporate vibration isolators into their battery mounting design. From a physical isolation perspective, the client was satisfied with our initial catalog product offering. However, they requested an additional solution with a very low level of electrical conductivity—a solution that would improve both system performance, reliability and operator safety. They would also need it fast, so we said, “give us two weeks.”
Diagnosing the Problem
The client originally chose us for vibration isolators because of our reputation as a solution provider with extensive materials expertise and in-house testing capabilities. When the need arose for mounts with greater electrical isolation--that is, lower conductivity than is common for rubber mount materials--Hutchinson’s material expertise came into play.
While we have extensive experience producing mounts with elastomeric materials spanning a range of conductivity levels, a mount capable of meeting the customer’s unique specifications did not exist in our product portfolio at the time. We considered an alternative option for electrical isolation at the mounting locations by introducing non-conductive insulating components between the vibration mounts and battery module. However, space constraints and assembly complexity precluded that option—meaning we would have to create a new compound to provide the necessary rubber electrical resistance. Additionally, the new part would need to be delivered within two weeks for the client to stay on schedule and build demonstrator trucks for customer exposure and feedback at an upcoming tradeshow.
Navigating the Challenges
Formulating a rubber compound to meet a specific requirement frequently leads to trade-offs between an elastomer’s various characteristics, including mechanical properties, environmental capabilities, durability, cost and more. Understanding the trade-offs and optimizing an elastomer compound to best meet the needs of the application is a Hutchinson core competency. Neither the customer’s nor our engineering team wanted to solve the conductivity challenge by creating a product with a significantly higher price point, shorter service life or other compromise. To best address this issue, Hutchinson and the client’s engineers worked closely to define the specific requirements needed for the desired outcome. The result: a compound focused on reduced electrical conductivity, with mechanical properties and environmental capabilities that would meet the expectations of the vehicle/transportation market.
Producing Results
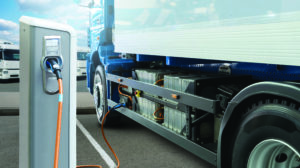
Ultimately, two different elastomer compounds were formulated, both incorporating our proprietary carbon nanotube technology to tailor the elastomer conductivity level and other properties. Then, two different sets of low conductivity prototype isolators were molded, in a unique shade of green, to identify them as high resistivity rubber mounts. The parts were installed on a development vehicle in the customer’s engineering lab and their performance was evaluated through a series of tests. In the end, the electrical resistance was remarkable, exceeding the requirements by a substantial margin. Furthermore, the entire process happened within two weeks to meet the customer’s schedule.
Both the process and results are indicative of Hutchinson’s capability to go above and beyond the competition in terms of determination and problem-solving as well as our ability to customize materials to meet special requirements. If your electric vehicle project needs a customized elastomer solution, our rubber development experience and expertise can get you there. Hutchinson—we make it possible.
Quick Contact Form
The personal data collected are processed, the responsibility of which is HUTCHINSON AEROSPACE & INDUSTRY INC. company, in order to respond to your request for information and/or for the purpose of commercial prospecting. Mandatory fields to be completed are marked with an asterisk. The legal basis for the processing is your consent, which you may withdraw at any time, without prejudice to previous processing operations. Personal data are reserved for the use of the HUTCHINSON group and may only be transmitted to companies of the HUTCHINSON group and/or commercial partners for commercial purposes, if you have expressly consented to this.
In accordance with the regulation relating to personal data (GDPR), you have the right of access, rectification and erasure of your personal data, as well as the right of opposition to their processing. You may request the disclosure of your personal data and you have the right to define guidelines for the treatment of your personal data after your death. You can also request the portability of your data as well as the limitation of their processing, and/or file a complaint to your local authority.
You can exercise your rights and ask us about the processing of your personal data by contacting us at the following email address: [email protected]
To find out more read our Privacy and Cookies Policy.
QUICK LINKS
- View Product Family
- Download Catalog
- Hutchinson Standard Anti-Vibration Isolators
- View Industrial Applications Matrix
The personal data collected are processed, the responsibility of which is HUTCHINSON AEROSPACE & INDUSTRY INC. company, in order to respond to your request for information and/or for the purpose of commercial prospecting. Mandatory fields to be completed are marked with an asterisk. The legal basis for the processing is your consent, which you may withdraw at any time, without prejudice to previous processing operations. Personal data are reserved for the use of the HUTCHINSON group and may only be transmitted to companies of the HUTCHINSON group and/or commercial partners for commercial purposes, if you have expressly consented to this.
In accordance with the regulation relating to personal data (GDPR), you have the right of access, rectification and erasure of your personal data, as well as the right of opposition to their processing. You may request the disclosure of your personal data and you have the right to define guidelines for the treatment of your personal data after your death. You can also request the portability of your data as well as the limitation of their processing, and/or file a complaint to your local authority.
You can exercise your rights and ask us about the processing of your personal data by contacting us at the following email address: [email protected]
To find out more read our Privacy and Cookies Policy.