Case Study
Automation: A Hutchinson Success Story
Like all manufacturers, Hutchinson was facing some formidable challenges. Material costs were rising. Labor was short in supply, in high demand, and getting pricier. Inefficiencies resulted in scrap and rework rates that management knew were too high. Consistent quality and on-time delivery were non-negotiable commitments to their customers, so the only reasonable option was to address inefficiencies, reduce error/waste, and maximize quality control.
GREAT PEOPLE achieving their FULLEST POTENTIAL helping to build a GREAT PLACE
Hutchinson’s company vision statement makes it clear—its commitment to its employees is non-negotiable. While the need to build greater efficiencies was a motivation, engaging employees with more meaningful, value-added work had to be a key result.
Innovation Born Out of Necessity
Enter the Automation Team, which was tasked with the formal mission to “seek and address opportunities where waste can be eliminated by reducing process variation and increasing quality consistency through automated processes and/or the implementation of innovative assist devices.”
The team is led by Dave Brushaber and includes engineers Bill Coffey and Andreas Askeland along with technician Jason Bourgoin Jr. Together, they took on the responsibility of evaluating processes across the organization and applying automation to achieve consistent quality and predictable throughput and increase the time employees are focused on value-added work.
Their first project was to address inefficiencies in the manufacture of a part made for one of Hutchinson’s largest defense sector customers, which required a team of operators to spend significant time manually cleaning off the flash and debris inherent to the molding process.
The team made use of a “cobot” (a robot designed to share space safely with a human operator). They customized the cobot for the task and built a cell in which it could complete the work safely, efficiently, and uniformly. The machine was named Cobot 1.0, and
it worked beautifully.
However, not long after it was deployed, the team realized that employees were still spending precious time repetitively cleaning the same part, removing excess adhesive with one brush, and then cleaning out the threads with another. The Automation Team went to work, developing what they dubbed “Cobot 2.0,” adding parts and functionality that could handle those tasks as well.
From that point forward, the team made sure to focus on three major pillars in any project they took on: flexibility, scalability, and portability.
“In our business, we build one part for a week and then switch over and build another part for two days,” says Dave. “We build 10 of these, 100 of those. The biggest challenge is finding the justification for a $20,000 piece of automation to solve a problem for a part that brings in a revenue of only $10,000 a year.”
The answer, Dave says, lies in three pillars. “We need a solution flexible enough to adapt to multiple applications, scalable to larger and smaller runs, and portable, so it doesn’t take up floor space when it’s not needed,” he said.
Efficiency is a Collective Effort
The success of these projects set the bar for the Automation Team’s ongoing success. They were able to identify specific goals that should be reached when considering automation to address inefficiencies and source variations that create scrap or engage employees in non-value-added work. These are improved consistency for lower production cost, greater production throughput per direct labor hour, reduction in human variation, and improved ergonomics to reduce repetitive motion incidents. When these goals are achieved, the Automation Team creates a greater capacity for the organization to take on additional high-ROI projects.
The other key goal was to free employees for more meaningful, value-added work.
“Sitting there with a pair of scissors, trimming rubber off a part, isn’t what most employees would consider a ‘great thing,’” says Dave. “Automation frees people from those repetitive minor tasks and allows them to focus on work that is more valued by our customers.”
That said, it took some time to earn workers’ trust. “When we first began introducing automation to some processes, employees were watching us very cautiously. Some employees wondered if we were going to eliminate their jobs,” Dave explains. “We told them that our automation objectives were to 1) help them become more productive while reducing repetitive motion, 2) help Hutchinson increase the quality consistency of the products that we produce and sell to our customers, and 3) increase the value-added content of their work. But we had to walk the talk. Employees had to see it for themselves. Once they did, they started to get really interested in what we were doing and saw how they’re being helped by our work.”
The team established a yearly automation summit for Hutchinson employees, inviting them to contribute ideas for greater efficiencies across the organization. Some solutions that emerged were impressively simple.
“We had these inkjet printers for ID marking of parts at our Ithaca facility,” Dave recalls. “Basically, the operator would put a part underneath the printer and move the part around by hand so it would ink stamp it in the right spot. We decided the solution was to set the part on a little belt conveyor. Now, the operator sets the part on the conveyor, it gets ink stamped, and drops into a box. Eloquently simple and effective!”
Another idea generated from the automation summit sprung from the production of generator mounts. These large mounts require six rubber blocks to be cold-bonded to the metal, and employees had to sand and prep the rubber surface by hand so it would properly bond to the adhesive. This required an operator to spend several minutes using an orbital vibrating palm sander to scuff each rubber part. The solution was a portable machine that pulled the rubber block past brushes that scuffed the part in under 10 seconds. The operators’ hands are saved along with hours of precious time.
Building on Success
So far, the Hutchinson Automation Team can only be described as a success story. Their innovation and automation efforts have resulted in a nearly $1 million improvement in productivity, and they’re on track to capture another $0.25 million by the end of 2023. Automation efforts have resulted in consistent higher quality of output, improved and predictable on-time delivery, improved ergonomics, and decreased injuries due to repetitive motion.
Employees produce more throughput while increasing the time they spend doing value-added work, creating consistent high value to the benefit of our customers. With less time spent on repetitive tasks and increased pay for quality consistency, jobs are more fulfilling and rewarding. Hutchinson continues to strengthen its competitiveness, and customers are benefiting from Hutchinson’s ability to consistently stay on schedule and deliver products that meet their quality requirements.
If you are interested in learning more about our capabilities, or if you want to speak with us about your project, we’d love to connect. Reach out today to learn more.
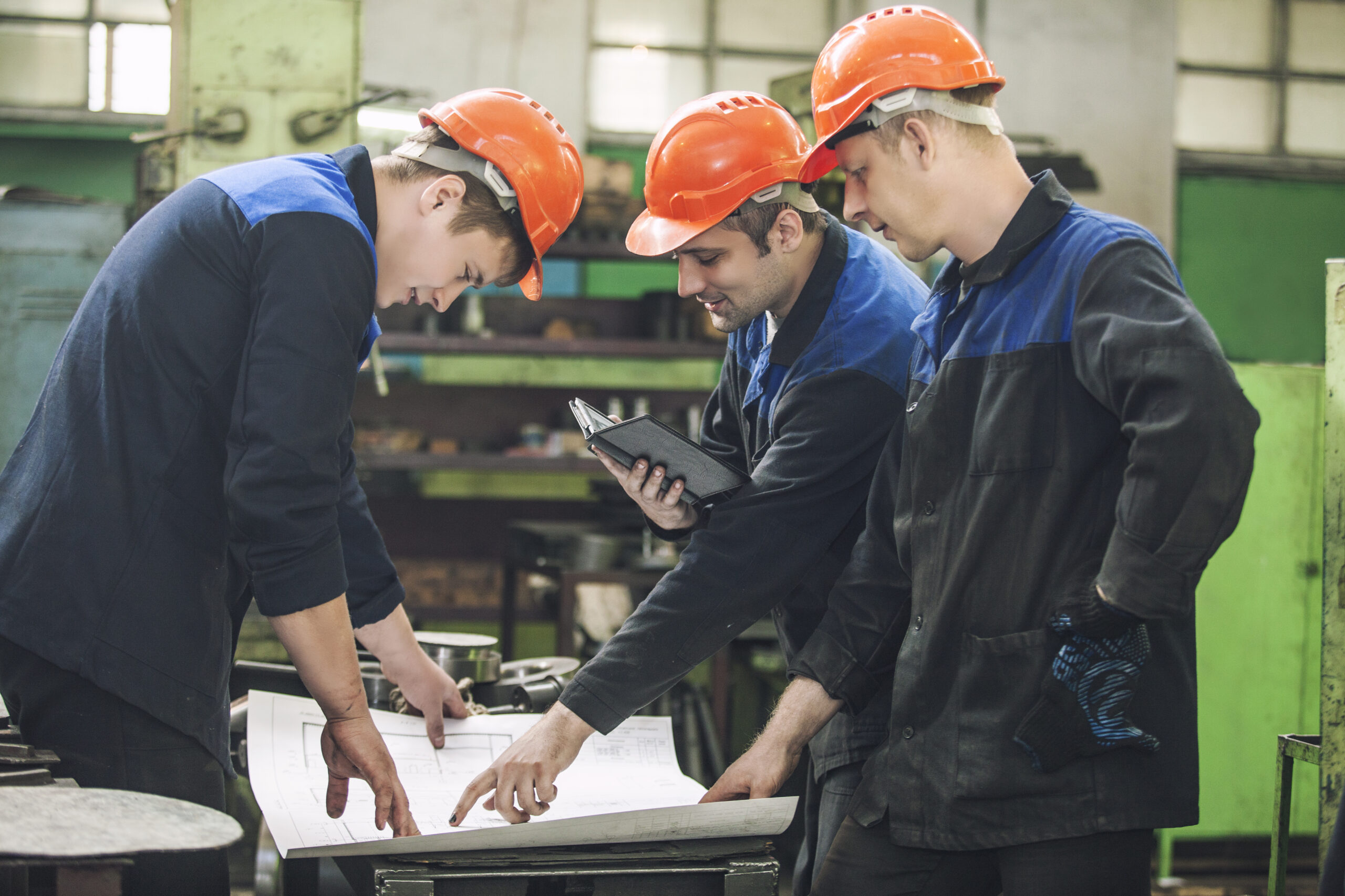
Quick Contact Form
The personal data collected are processed, the responsibility of which is HUTCHINSON AEROSPACE & INDUSTRY INC. company, in order to respond to your request for information and/or for the purpose of commercial prospecting. Mandatory fields to be completed are marked with an asterisk. The legal basis for the processing is your consent, which you may withdraw at any time, without prejudice to previous processing operations. Personal data are reserved for the use of the HUTCHINSON group and may only be transmitted to companies of the HUTCHINSON group and/or commercial partners for commercial purposes, if you have expressly consented to this.
In accordance with the regulation relating to personal data (GDPR), you have the right of access, rectification and erasure of your personal data, as well as the right of opposition to their processing. You may request the disclosure of your personal data and you have the right to define guidelines for the treatment of your personal data after your death. You can also request the portability of your data as well as the limitation of their processing, and/or file a complaint to your local authority.
You can exercise your rights and ask us about the processing of your personal data by contacting us at the following email address: [email protected]
To find out more read our Privacy and Cookies Policy.