Case Study
Passenger Railcar Airbags:
A Hutchinson reHuse Success Story
Manufacturers are facing increasing challenges that include the growing necessity to deliver products meeting sustainability expectations while reducing product selling prices despite escalating labor, energy and material costs to produce them. Hutchinson Aerospace and Industry is addressing the seemingly conflicting challenges with a recently launched program called Hutchinson reHuse.
Across several markets, Hutchinson supplies shock and vibration solutions that require adhering and molding elastomeric materials to large metal components. The metal components are expensive and involve environmentally unfriendly processes to produce.
Even with significant developmental advances in the durability performance of Hutchinson supplied elastomers, most often the useful life of the metal components used in products produced by Hutchinson far exceeds that of the elastomer. The Hutchinson reHuse program recovers and refurbishes customer-supplied used parts.
Once received, the recovered used parts are cleaned, leaving only the original metal component, ready to be processed into a new part. The Hutchinson-produced reHuse new parts meet all customer original product specifications, eliminate the negative environmental impact from producing new metal parts, and (because metals are recovered) reduce the overall Hutchinson cost of manufacturing. Consequently, Hutchinson can offer reHuse products that help their customers achieve their financial objectives.
Passenger Railcar Application
Hutchinson’s most recent success story was achieved with one of its large railcar customers. Passenger railcar airbags are integral to the car’s suspension system. Unlike those in an automobile, passenger railcar airbags help make sure the ride is smooth and the train’s car floor is aligned with the height of the platform where passengers board.
When it came time to overhaul the passenger cars, the municipality operating the railcars concluded that the airbags needed to be replaced. After competitively bidding the overhaul work needed, the municipality contracted with one of Hutchinson’s customers to complete the overhaul. Municipalities prioritize both quality of work and cost when selecting who they contract with to complete necessary overhauls.
Passenger railcar airbags are highly engineered, complex and consequently expensive. Each passenger railcar requires four airbags. The project involved overhauling a total of 600 railcars or purchasing 2,400 airbags. When the customer called Hutchinson, they were seeking cost-effective solutions to meet the municipality’s overall overhaul approved budget. That’s when Hutchinson’s reHuse initiative came into play.
For this overhaul project, the Hutchinson team was able to recover and refurbish large metal components used to produce an airbag; airtight top plate, emergency spring and large castings.
“We had been developing the reHuse process and process controls for the past two-years,” said Tom Robinson, Hutchinson’s Railroad Market Segment Manager. “As the green movement and Hutchinson’s overall commitment to sustainability have grown, we wanted to increase and refine our reHuse program capabilities. We’re working to do our part for our customers and our planet.”
Benefits and Savings
Across the board, the reHuse initiative is all about helping customers meet their financial, turnaround and sustainability objectives. For this overhaul project, Hutchinson’s customer saved $1.2M, shortened the time required to complete the overhaul project and environmentally reduced both production treatment waste and CO2 by an estimated 40% versus producing airbags with previously unused metal components.
What wasn’t reduced was Hutchinson’s focus on quality.
“Rider comfort and safety depend upon these parts, so quality remains the top concern,” Robinson said. “We test each reHuse part 100% under pressure, exactly as if it included previously unused metal components. Our Quality Assurance department verifies that each part is within spec. We will not let a part leave Hutchinson’s production area without passing final/production testing.”
Vision for the Future
With the completion of this first large-scale reHuse success story, the team is already working with customers on other new opportunities that meet the criteria of positive environmental impact, quality assurance and competitive pricing.
To learn more, request a quote, or discuss reHuse options for your next project, contact us.
The Recovery Cycle
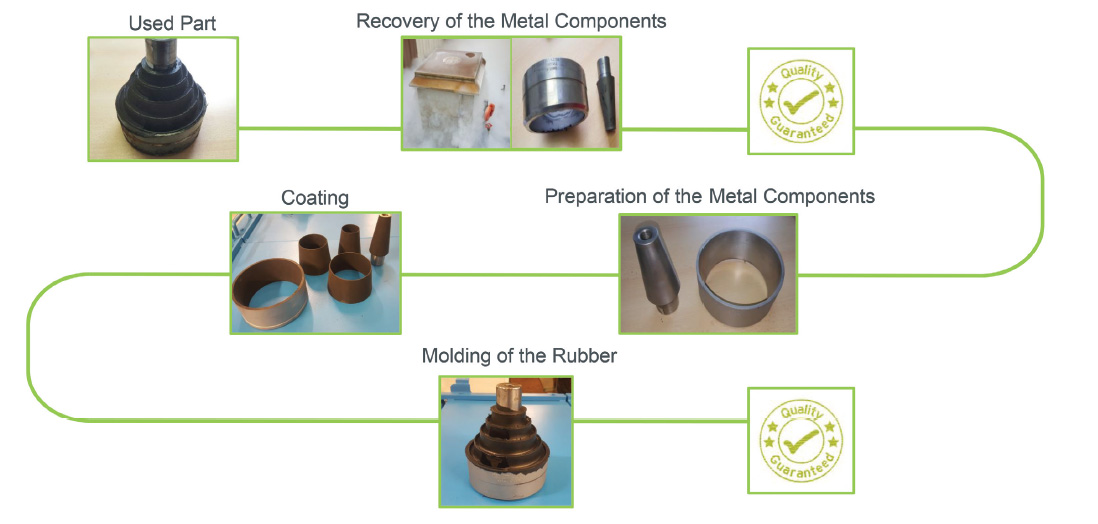
If you are interested in learning more about our capabilities, or if you want to speak with us about your project, we’d love to connect. Reach out today to learn more.
Quick Contact Form
The personal data collected are processed, the responsibility of which is HUTCHINSON AEROSPACE & INDUSTRY INC. company, in order to respond to your request for information and/or for the purpose of commercial prospecting. Mandatory fields to be completed are marked with an asterisk. The legal basis for the processing is your consent, which you may withdraw at any time, without prejudice to previous processing operations. Personal data are reserved for the use of the HUTCHINSON group and may only be transmitted to companies of the HUTCHINSON group and/or commercial partners for commercial purposes, if you have expressly consented to this.
In accordance with the regulation relating to personal data (GDPR), you have the right of access, rectification and erasure of your personal data, as well as the right of opposition to their processing. You may request the disclosure of your personal data and you have the right to define guidelines for the treatment of your personal data after your death. You can also request the portability of your data as well as the limitation of their processing, and/or file a complaint to your local authority.
You can exercise your rights and ask us about the processing of your personal data by contacting us at the following email address: [email protected]
To find out more read our Privacy and Cookies Policy.
reHuse:
Eco-Responsible Maintenance
Hutchinson’s reHuse initiative is based on three pillars: positive ecological impact, quality assurance, and competitive prices.
Here’s how it works. Hutchinson:
- Takes the used rubber-to-metal parts
- Recovers and inspects the metal components, discarding the contaminated rubber, which becomes brittle and unusable over time
- Prepares and coats the metal components
- Molds and attaches new rubber components
- Tests each part to ensure it performs to the highest standards